Chemical Plant Flange Preparation Machine for Maintenance
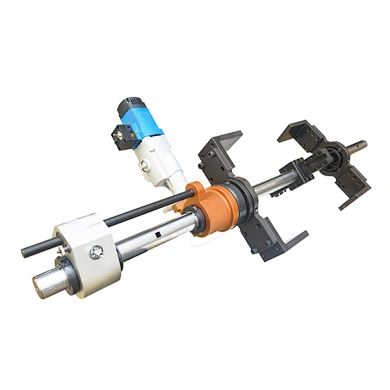
,文章长度在1000字左右
html
Chemical Plant Flange Preparation Machine for Maintenance
In the demanding environment of chemical plants, maintaining equipment is critical to ensure operational efficiency and safety. One of the most crucial aspects of maintenance involves flange preparation, which ensures proper sealing and connection of pipelines. A Flange Preparation Machine is an indispensable tool for this task, offering precision, speed, and reliability in preparing flanges for welding or gasket installation.
Why Flange Preparation is Essential in Chemical Plants
Chemical plants operate under extreme conditions, including high pressure, corrosive substances, and elevated temperatures. Flanges, which connect pipes, valves, and other equipment, must be perfectly prepared to prevent leaks, contamination, and potential hazards. Poorly prepared flanges can lead to:
- Leakage of hazardous chemicals
- Equipment failure and downtime
- Increased maintenance costs
- Safety risks for workers
A dedicated Flange Preparation Machine ensures that flanges are machined to exact specifications, providing a smooth, clean surface for optimal sealing.
Key Features of a Flange Preparation Machine
Modern flange preparation machines are designed to handle the rigorous demands of chemical plant maintenance. Some of the key features include:
- Portability: Many machines are compact and lightweight, allowing technicians to bring them directly to the job site.
- Precision Cutting: Advanced cutting tools ensure smooth, burr-free surfaces for perfect flange alignment.
- Versatility: Capable of handling various flange sizes and materials, including stainless steel and carbon steel.
- Efficiency: Reduces preparation time significantly compared to manual methods.
- Safety: Minimizes the need for grinding or welding, reducing exposure to sparks and fumes.
How a Flange Preparation Machine Works
The process of preparing a flange using a specialized machine involves several steps:
- Inspection: The flange is examined for damage, corrosion, or irregularities.
- Mounting: The machine is securely attached to the flange using clamps or magnetic bases.
- Cutting/Facing: A rotating cutting tool removes imperfections and creates a smooth, flat surface.
- Deburring: Any remaining rough edges are smoothed out to ensure a perfect seal.
- Final Check: The flange is inspected again to confirm it meets required tolerances.
Benefits of Using a Flange Preparation Machine
Investing in a high-quality flange preparation machine offers numerous advantages for chemical plant maintenance teams:
- Improved Seal Integrity: Properly prepared flanges reduce the risk of leaks and fugitive emissions.
- Extended Equipment Life: Reduces wear and tear on gaskets and bolting systems.
- Cost Savings: Minimizes downtime and reduces the need for frequent repairs.
- Enhanced Safety: Eliminates manual grinding risks and ensures compliance with industry standards.
- Consistency: Delivers uniform results across multiple flanges, improving overall system reliability.